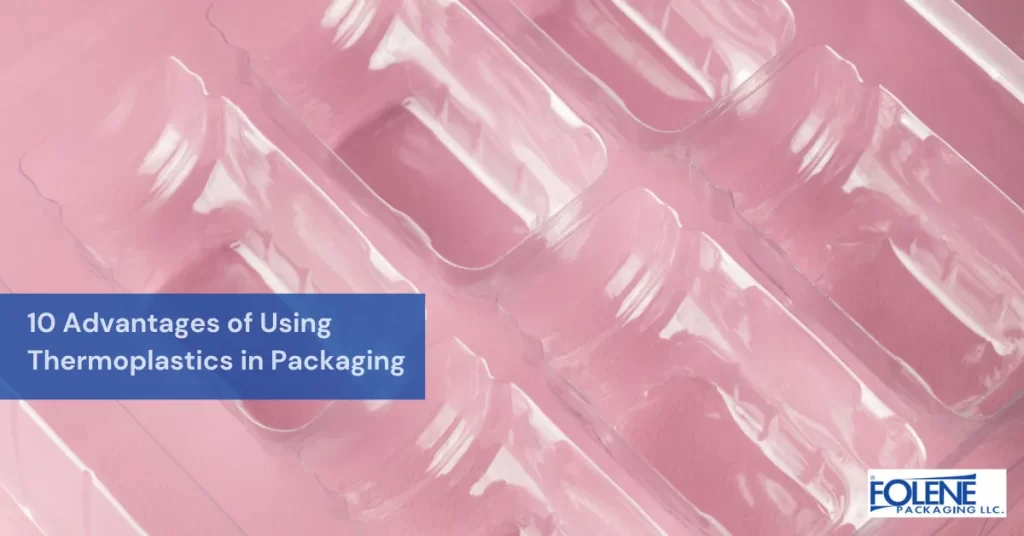
The world of packaging offers suppliers many options. They must choose the right vendor who understands their need for quality packaging and knows its strengths. For suppliers, packaging that offers integrity, protection, and good value affects the distribution and sale of the products and, ultimately, the profit margin.
Understanding the properties of packaging materials can be pretty technical. So, knowing the characteristics of thermoplastics makes all the difference in ensuring the successful packaging of your products from the very beginning of the supply chain.
What Are Thermoplastics?
Thermoplastics, as their name suggests, are materials that change when they are heated, and that is when they can be shaped. What is thermoplastic? “Thermoplastic” means heat and pliability, and a thermoplastic material is a soft material when heated, and it hardens when it cools. After heating and shaping, thermoplastics remain “plastic” – they can be heated and re-molded repeatedly, such as by injection molding. The opposite of a thermoplastic material is a thermoset material. The main difference between thermosetting vs. thermoplastic polymers is that thermoset polymers cannot be reshaped once the material has hardened.
Define Thermoplastic
Thermoplastics are a type of polymer. Polymers can be natural or synthetic substances that have large molecules composed of repeating units (monomers). Different polymers have distinctive properties depending on how their monomers are arranged. For example, with crosslinks in polymers, the tridirectional covalent bonds make a very strong polymeric material that produces a strong, light form of packaging.
Where Are Thermoplastic Materials in Packaging?
Thermoplastic materials are used everywhere in packaging. According to research, the food packaging industry utilizes 84% of thermoplastics. But let’s see how other thermoplastic materials are used in packaging. The polymers we use for packaging are categorized and coded from 1 to 7, with a symbol similar to the recycling symbol and a number inside. This label is the Resin Identification Code (RIC), which identifies the polymeric types of resin used in the packaging.
Here are some common thermoplastic materials with their RIC labels and their uses in packaging:
RIC #1: Polyethylene (PE)
Polyethylene is used in packaging for large, heavy items and packaged goods in bags of all shapes and sizes. Polyethylene is used for zip-lock bags, plastic bottles, disposable food and drink containers, personal wellness packaging, food packaging crates, stretch film, packaging tape, transportation pallets, and plastic sheeting. 2021 was the year that polyethylene usage peaked. Chem PMC says in 2023, the U.S. and Canada used ‘just’ 2.5 million metric tons (MMT) of LDPE, 4.8 MMT of LLDPE, and 6.8 MMT of HDPE.
Polyethylene has many subtypes, such as linear low-density polyethylene (LLDPE), which is used to make plastic bags and other types of food packaging, and, the widely used polyethylene terephthalate (PET, PETE).
RIC #5: Polypropylene (PP)
Polypropylene is used in pharmaceutical packaging, strapping tape, flat bags, gusseted bags, instead of paper by choice, cellophane packaging, reusable food packaging, ready-to-eat meals, dairy products such as sour cream and yogurt, and microwaveable containers.
RIC #3: Polyvinyl Chloride (PVC)
PVC uses include plastic bags, wrappings for frozen foods, lids, and stretch films for meat, cheese, bakery products, and healthcare products. The ECVM reports that 3.7% of total PVC production (over 400,000 tons) is used in packaging in Europe annually. PVC has its pluses, but a minus is the incorporation of the vinyl chloride monomer, which is associated with health risks.
RIC #7 Other: Acrylic
Acrylic is used in cosmetics packaging, such as skin-care products, in plexiglass format. Acrylic-based paints are used for road markings and as emulsions for sealing lacquers used in coating solutions, such as for the insides of beverage cans.
RIC #7 Other: Polycarbonate (PC)
Polycarbonate is used in packaging for plastic water bottles and reusable food storage containers.
RIC #7 Other: Nylon
Nylon is used to package perishables (e.g., meats and cheeses) that are ready-to-eat or semi-prepared.
Why Are Thermoplastic Polymers Important in the Packaging Industry?
Many thermoplastic material packaging options are available to suppliers, each with different characteristics. Once suppliers clarify their packaging needs, they can easily access suitable packaging. Additionally, thermoplastic polymers support global environmental initiatives, enabling manufacturers to comply with international ecological requirements.
The production of thermoplastic resin is established and stable. The market is extremely developed since polymers are extensively used for packaging. Globally, the thermoplastics market is expected to grow to $49.4 billion by 2032, at a CAGR of 6.5% from 2023 to 2032.
10 Packaging Advantages of Thermoplastics
The benefits of thermoplastics are well known as thermoplastics offer numerous packaging advantages to suppliers, producers, and e-commerce marketers:
1. Thermoplastic Materials Are Lightweight
Polypropylene is one of the lightest thermoplastics and is popular for packaging everyday household items. Cleaning products and medical items can be stored in lightweight packaging, which reduces shipping expenses. Manufacturers also save on costs when transport expenses are reduced through efficient processing.
2.Thermoplastic Polymers Are Protective
The toughness and flexibility of thermoplastics protect products during packaging and shipping against knocks and scratches, moisture-related damage, and tampering. This protection is critical in the electronics and medical industries.
3.Thermoplastics Are Customizable
Thermoplastics can be designed to package and fit almost any product. This makes the customization of packaging very doable. Thermoplastic wrappings can be any color, shape, size, or density that suppliers need. Suppliers can determine which type of packaging markets best and select the best concepts. Suppliers can customize thermoplastics by adding a polymer coating, such as an anti-static coating or anti-microbial finish. Packaging can be upgraded with carefully designed coloring and texture finish added to the packaging’s exterior.
4.Thermoplastics Offer Toughness and Strength
Thermoplastics demonstrate an impressive tensile strength compared to metals such as aluminum and steel. Impact testing or puncture-resistance testing reveals the tensile strength of packaging and films made of thermoplastic materials. PVC and polycarbonate are two types of thermoplastics known to be tough and durable.
5. Thermoplastics Are Versatile
The raw material can be shaped through thermoforming or injection molding. It can be shaped in any dimension, allowing manufacturers and suppliers to choose from diverse packaging types and designs.
6.Thermoplastic Resin Can Be Recycled
When thermoplastics are heated, their physical properties change as the material changes from solid to liquid, but the chemical composition remains the same. No chemical bonding takes place, so the production process is reversible. This allows thermoplastics to be recycled. Depending on the additives used in the production process, some thermoplastics are easier to recycle than others.
7.Thermoplastic Polymers Are Sustainable
Using thermoplastics can reduce garbage and plastic waste wherever the plastic is reused. Potentially, some thermoplastics can be recycled indefinitely with no risk of degradation.
8.Thermoplastics Are Corrosion Resistant
Thermoplastics are highly resistant to chemical distortion, maintaining their physical integrity by design. The thermoplastic film used in packaging is one way of protecting corrosion-sensitive products.
9.Thermoplastic Materials Are Food Safe
Many types of thermoplastics are food-safe, with the resistance to wear and impact, strength, and dimensional stability typical of thermoplastic serving food-related purposes well.
10.Thermoplastics Are Flexible
Thermoplastics are flexible – the degree of flexibility of elasticity depends on the additives used in production. When comparing thermosets vs thermoplastics, thermosetting plastic is a brittle plastic polymer. Some types of thermoplastics are known as thermoplastic elastomers (TPEs). These include:
- styrene block copolymers (TPE-S )
- thermoplastic vulcanizates (TPV), and
- thermoplastic polyolefins (TPO),
each of which has its specific applications.
Folene Packaging’s Thermoplastics: A Full Range of Polymer Plastic Films
Folene Packaging provides high-quality shrink films – made of excellent, protective, and economical plastic polymer material – in a wide range of gauges and types, which are used for packaging a comprehensive range of products. Many kinds of thermoplastic film are used in packaging, and suppliers only need to choose the one that suits their packaging and product needs the best.
Folene Packaging gives its clients a professional and efficient service and helps them select the best type of polyolefin thermoplastic film. Folene Packaging is the right vendor for shrink films as our skilled and experienced account managers can guide you through your planning stages as you learn more about polyolefin shrink films or help you choose the film that matches your needs best, whether it is the Flxtite® regular polyolefin range or the Ecolene® biodegradable polyolefin range.
Contact Folene Packaging to learn more about successful packaging with thermoplastics.
FAQs about Thermoplastics
Why are thermoplastic films used for packaging?
Products covered with thermoplastic films are protected from contamination, are tamper-safe, and have longer shelf lives. The film material also improves shelf appeal, as the glossy, clear film enhances the product’s appearance. Additionally, thermoplastic films support branding, as manufacturers can print marketing or product information on them.
What is one difference between thermoplastic and thermosetting plastic?
The main difference is that thermosets strengthen when heated, and thermoplastics become softer when heated. This makes amphorous materials – thermoset plastic polymer materials – excellent for heat-resistant medical equipment. Thermoplastic materials are crystaline materials and are heat sensitive – semi-crystalline thermoplastics melt when exposed to heat (each form of thermoplastic material has a different melting point.) Thermoplastic composites soften and can become molten or viscous, depending on the number of ‘arms’ in the crystalline structure – this is at the molecular level. However, both thermosets and thermoplastics boast chemical resistance.
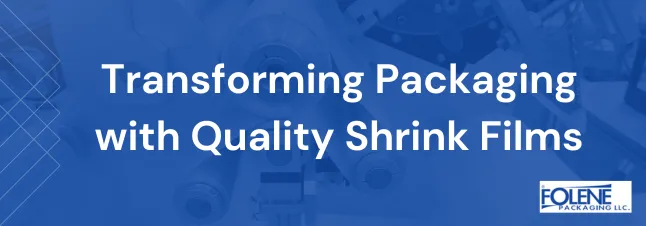