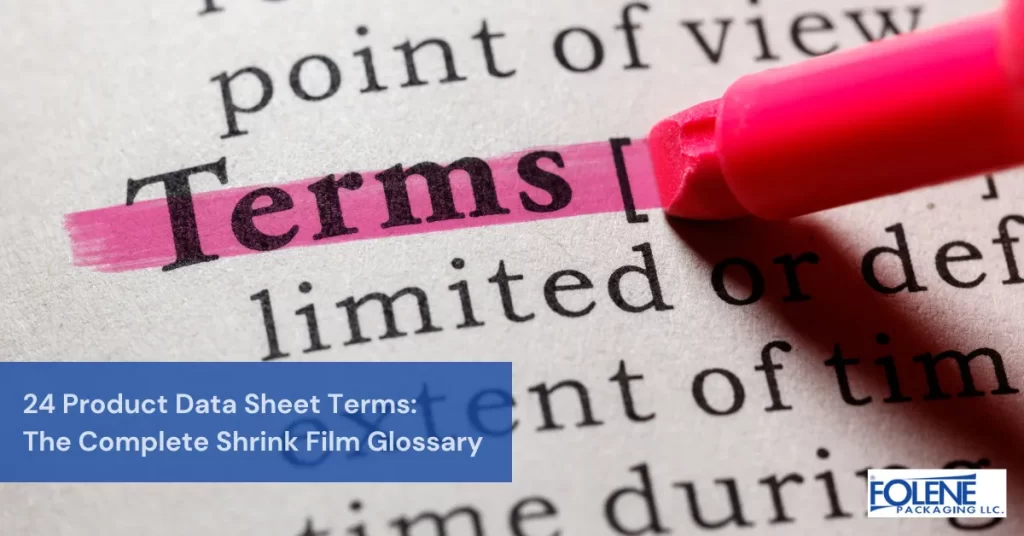
How to Understand a Product Data Sheet About Flxtite® Shrink Films
Folene Packaging understands consumer needs for various types of film packaging. We ensure that our products meet users’ desired specifications and the highest quality standards. The result is high-quality shrink-packaging products that match user requirements. We describe each product’s specifications clearly in the product data sheet so that our customers know what they are buying and can expect the best results for each application.
However, a product data sheet is, by definition, a technical data sheet that uses many technical terms. In this post, we will break down the technical terms used in a product data sheet to ensure product compatibility before ordering packaging film.
Why Should Manufacturers Learn the Terminology of a Product Data Sheet?
Manufacturers need to understand the concepts and terminology presented on a technical sheet – in an industry where different names are commonly used for basic technical terms.
Understanding the terms on a product specification sheet allows suppliers to answer the question: “How does shrink wrap work?”
When suppliers comprehend the polyolefin shrink film manufacturing process:
They can avoid costly mistakes
Their experience while working will be smooth, satisfying, and enjoyable
They can take advantage of more efficient operations.
Not Understanding The Product Data Sheet Can Cause Issues
Manufacturers who do not invest in understanding the product data sheet for the packaging they are using could be letting themselves in for experiencing:
frustration, anger, and tension in the workplace
expensive mistakes in the packaging process
supply-chain issues such as delays and upset clients
3 Examples of How Understanding Technical Terms of the Product Data Sheet Saves Wasted Expenses
By reading product data sheets carefully, manufacturers can ensure that processes will go more smoothly when their workers are on the factory floor. Time, space, and raw materials are some of the capital costs a manufacturer or packager must expect but does not want to waste. Technical data sheets show all the essential information in sufficient detail to decide which film to use.
Crosslinks in polymers are one example of how knowing the terminology allows manufacturers who need packaging to buy stronger shrink wrap that is more suitable for wrapping their products. By properly understanding the characteristics of the packaging film, operators can:
1. Avoid insufficient shrinking by using the correct heat and size of the film
Use a packaging machine that offers the correct heat settings for your wrap. Check that your shrink gun, machine, or tunnel is hot enough. Ensure the film width is not too wide. Otherwise, annoying, sharp and scratchy “dog ears” may form at the ends of the package. This common problem can be avoided by choosing the correct film width and knowing the shrinkability of the film before you begin to package the product.
2. Avoid tears in shrink packaging
Ensure that the shrink film you use has an acceptable elastic limit level so that heat and pressure can be applied without the wrap snapping.
A manufacturer must know a packaging film’s yield point and yield strength before loading it into the machine. Using the correct type of film will prevent tears.
The film tensile strength limit tells the user how much force can safely be applied when packaging. Packaging operators must use this information carefully to prevent tears.
3. Avoid running out of supplies in the middle of wrapping products
Part of using shrink film for packaging products is understanding the shrinkability rate of the film. This helps users to calculate how much film they will see when packaging an order. Once you know how much film one item takes, you can calculate how much the entire batch will require. If there is a miscalculation due to not knowing how much the film will shrink and how much you need to use altogether, you could end up with an order half-wrapped and not enough film in stock. Conversely, an order could be completed, but excess rolls of shrink wrapping were purchased for no use.
List of 24 Glossary Terms:
A glossary of terms for shrink films contains many technical specifications. Many of these are performance data within a range or a specific typical value. A technical data sheet contains detailed information, but what is included is at the discretion of the manufacturer of the product, unlike material safety data sheets that are guided by industry standards. Let’s look at some of the terms used in a typical Folene Packaging product data sheet:
1. Gauge
This measures the thickness of the shrink film in “gauge” or for polyethylene in “mil” ( 1 mil = 1 inch divided by 1000). It is sometimes measured in microns (gauge divided by 4 = a micron measurement).
A film gauge (thickness) of 80 is thicker than a gauge of 60. The most common gauges are 60, 75, and 100, although you can buy thinner or thicker film. A shrink wrap thickness guide helps guide users to the right film to use. If you are unsure which gauge of film is right for your product, we advise consulting with a representative who can guide you to the correct gauge of film for your packaging success.
2. Density
The density of ashrink wrap is measured by mass divided by volume. Film density measurement is expressed in gm/cc, which means gram per cubic centimeter. The film density affects how the film shrinks. Polyolefin films (POF) shrink consistently around the item with a lower shink force and at lower temperatures.
3. Yield
Yield is the value that tells you how much coverage you will get for each unit of roll weight. It is measured in square inches per pound (sq.in/lb). Understanding yield can help reduce waste and cost as you choose the most suitable film for your needs. (Be careful not to confuse Yield for Yield Strength).
4. Roll Weight
Roll weight is the next value due to its connection with yield (above). It is expressed in pounds of roll weight per inch (lbs./in). Using the correct size of shrink film roll ensures that the products will be covered well without wasting as little as possible of the shrink film on the roll.
5. Haze
Film haze means the cloudiness of the shrink film, you may be more familiar with the word opacity. This measures how see-through the film is. Film haze measurement is often expressed as a percentage. The lower the value, the clearer the film. A low haze is required for products with a high desired level of visibility (the shrink wrap displays the product in a way that attracts attention). For products that are private, a less clear (high haze or opaque) film would be used.
6. Gloss
The gloss measure is expressed in “%@XX degrees,” which means how much light the shrink film will reflect from a light shone at it at a certain angle. XX is typically 45 degrees or 60 degrees. For some products, the glossiness of the wrapping improves the product’s appearance, color, vibrancy, and shelf appeal. Some studies suggest that glossy packaging attracts consumers because of its similarity to water, but matte packaging indicates healthier food in the packet. So, gloss is an important choice when determining packaging.
7. Coefficient of Friction, or COF
COF measures the slipperiness of shrink film. Additives can reduce slipperiness. High slipperiness complicates processing in high-speed packaging machines. Whether low COF is needed depends on the product and packaging method. A higher COF number indicates less slipperiness. COF is measured by placing two flat film samples together with a standard weight to assess friction.
8. Shrink Air Temperature
Since the nature of shrink wrap is that is shrinks under hot conditions, the shrinkage must be done right. This measures the heat of the air in the tunnel at which the film shrinks properly.
9. Free Shrink
Free shrink refers to the amount and ability of the film to shrink uniformly around the product before it comes into contact with the product (and ceases to shrink). Where there is free shrink it means the film will settle nicely and titidly around your product. Free shrink (also known as shrinkage or unrestricted shrink) is measures the shrinkage rate as a percentage of how much the film shrinks at a certain temperature (% @ 250F).
It is also called linear thermal shrinkage since it measures the linear dimensional change.
10. Shrink Force
This is measured in g/in or grams per inch. It determines the “shrink tension” level -the force that builds up while the film is shrinking. The gentleness or aggressiveness of how the film shrinks affects its performance.
11. Modulus of Elasticity
Modulus measures the stiffness of the film. This is tested by ASTM test D-882B, which tests for strength and elongation. Modulus is measured in KPSI or PSI (pounds per square inch, thousands).
The modulus is measured in elasticity in two directions of the film. MD and TD represent the machine direction and the cross direction (transverse direction) in which the shrink film is tested. For this reason, Modulus gives two numbers as the value, one for each direction of testing.
12. Tensile Strength (or Yield Strength)
MD and TD tensile strength measures how much force can be applied until the pressure breaks through the film. It is also called the yield limit.
Tensile strength is also measured in two directions of the film. MD and TD again represent the machine direction and transverse direction (cross direction) in which the shrink film is tested for tensile strength. For this reason, Tensile strength also gives two numbers as the value, one for each direction of testing.
13. Elongation At Break or Yield Point
This is the limit of “elastic behavior” when a film is stretched to the point that it will become “plastic” or permanently deformed. This is expressed as a percentage.
14. Water Vapor Transmission Rate (WVTR)
This measures how much water vapor can transfer from a sealed product over 24 hours. It is expressed as ge/100in/24 hours or g/meter squared/24 hours. Certain products need better isolation, and others need breathable films (food packaging). This term is also known as MVTR or moisture vapor transmission rate.
15. Oxygen Transmission Rate (OTR)
This measures how much oxygen can transfer from the sealed product over 24 hours. It is expressed as cc/100on/24hour. Certain products need better isolation, and others need to “breathe” a little.
16.CO2 Transmission Rate
Where relevant, ASTM D1434 tests for gas permeability for carbon dioxide and other gasses through plastic film and sheeting.
17. Minimal Use Temperature
For shrink films that are sensitive to cold, the measurement states the minimum temperature at which it is effective and safe to use the film.
18. Maximum Storage Temperature
For shrink films that are sensitive to heat, the measurement states the maximum temperature at which it is effective and safe to use the film.
19. PCR Content
This states the material composition as a percentage of post-consumer recycled content or recycled material included in the shrink film resin. Eco-friendly and sustainable shrink wraps are growing in popularity and availability as the use of PCR is improved (and a test will be developed by ASTM). More companies are turning our films with PCR content that can be up to 100% PCR content in shrink films.
20. Singlewound Roll Lengths
This is measured in feet per roll. There are commonly used lengths for the packaging film. Notice that the roll weight in any range of shrink films might be the same for each film gauge. So, thinner gauges tend to have longer rolls.
21. Centerfold Roll Lengths
Rolls folded down the middle for double-strength packaging wrap are about half as long as regular rolls. This is measured in feet per roll.
22. and 23. Single wound Roll Widths and Centerfold Roll Widths
Each company offers its typical range of widths for single-wound or centerfold-wound film, measured in inches.
24. Product Data: Factory Testing Disclaimer
The POF shrink film is tested to provide the values we list in the product data sheet. The technical information presented offers a brief description that is gathered through ASTM International testing (used to be known as the American Society for Testing & Materials), whose standards are relied upon worldwide. ASTM International proudly states that over 12,000 ASTM standards are used to test products globally. Nevertheless, all customers are advised and encouraged to perform thorough tests for their intended use and product marketing.
Folene Packaging Helps Suppliers Choose the Best Shrink Films By Having Accurate Product Data Sheets
Folene Packaging presents a full range of all types of shrink wrap for packaging edible and non-edible products of all shapes and sizes. Folene Packaging prides itself on the product data sheet it makes available to suppliers, who examine their packaging options. Folene packaging experts can expertly advise suppliers on which shrink film is the best option for the product. We understand the specifications of our shrink films.
We understand the details of the supply chain and the packaging it requires. Since Folene Packaging produces shrink films in the U.S. with European-grade raw materials, we can process orders in as little as two days!
Contact Folene Packaging and ask for our product data sheet for a full, expertly guided shrink-wrapping experience.
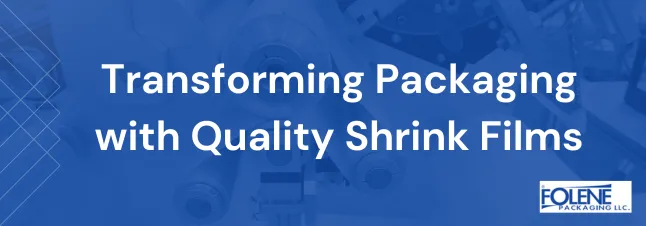