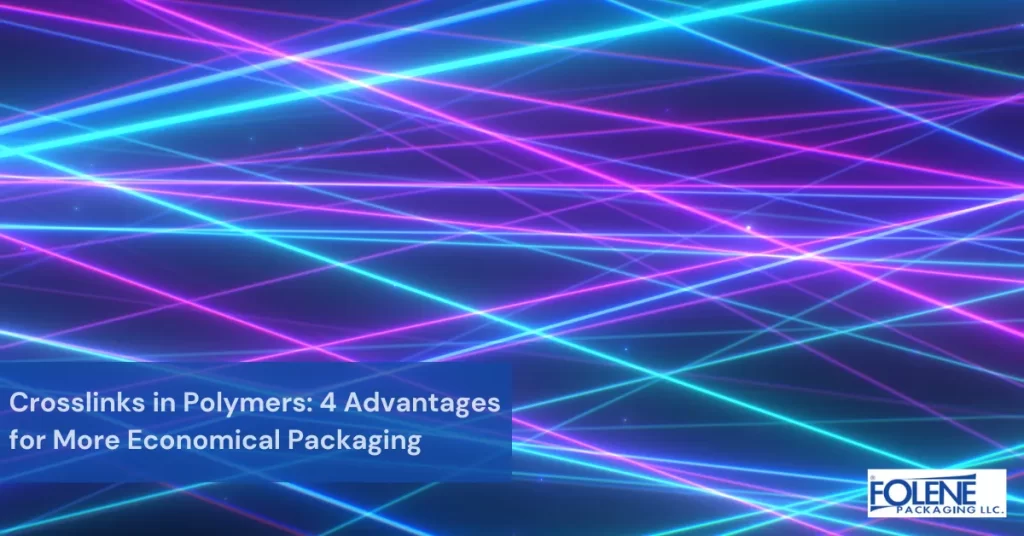
Manufacturers and distributors invest more than money when choosing packaging for their products. It’s an investment of time and energy and an expression of trust too. The purchasing department hopes the packaging materials will hold and protect the product until the end user discards the packaging. Cross linking is a feature that significantly improves packaging made from polymers.
The Vice President of Purchasing, the Director of Material Procurement, the General Manager, or the company owner must understand the benefits of their product’s packaging materials. Being informed is essential for all types of packaging materials. However knowledge is most important when using polyolefin shrink film, where fascinating and (invisible to the eye) cross linking gives it its strength.
What are Crosslinks in Polymers?
Crosslinks in polymers are an attribute of plastic materials. Let’s understand, what is crosslinking?
Cross linking can be defined as causing atoms, such as those in polymer chains, to link one polymer chain to another in a way that increases stability. The best way to describe crosslinked polymers is that they have a three-dimensional network of interconnected polymer chains on the atomic level.
Interatomic linkage is made to happen through chemical reactions (such as free radical polymerization), creating covalent bonds also called chemical cross-links, or physical cross-linking (such as hydrogen bonding). Monomers become polymers when polymer additives (or crosslinking agents) known as stabilizers and plasticizers are added, as well as impact modifiers and or flame retardants. By cross-linking a polymer and adding chemicals to the raw resin, we can improve the characteristics of the packaging material.
Generally, cross linking polymers offers better:
Processability – there is increased rigidity
Life span – the material becomes harder
Physical and chemical properties – the product has a higher melting point
How Do Crosslinks in Polymers Affect The Way We Wrap Merchandise?
Cross linked polymers definitely affect the way we wrap and ship products. When using shrink wrap for example, we cen reduce shrink film thickness, so we use less plastic to wrap more items. This is due to the improvements in tensile strength and durability provided through crosslinking. This is truly a connection between better packaging and lean operations.
Cross linking has been around since 1839 when Charles Goodyear experimented with the addition of sulfur to a plastic resin and discovered cross-linking also called vulcanization. Since then, the amount of plastic we produce – and dispose of – has increased drastically. Worldwide production of plastic in 2022 was 400.3 million metric tonnes. The more international markets grow, the more plastic packaging gets used, from 2021 to 2022 there was a 1.6% increase in plastic used.
Manufacturers and distributors seek policies to reduce the mass of plastic they are using. Thinner crosslinked plastic is much stronger than non-crosslinked plastic. So, using cross-linking polymers in packaging means less plastic will be used. Plastic of a lower gauge (thinner) has been shown in stress testing to outperform regular shrink packaging of a higher gauge (thicker).
4 Economical Advantages to Packaging With Crosslinked Polymers
Packaging comprised of crosslinked polymers is more stable, reliable, and predictable. This translates into real benefits and financial gains for producers and could help avoid or reduce plastic tax payments.
Packaging directors must always test thoroughly using packaging strength testing procedures to determine packaging that offers the highest packaging integrity and uses the fewest resources.
Crosslinked shrink packaging can bring these advantages:
1.Reduce Capital Expenses
Plastic wrap thickness is reduced. Gauges with lower mil thickness mean more wrap on the roll, so users get more for their investment.
A cross linked polymer renders a stronger wrap, which means it’s easier to process with fewer mechanical jams.
2. Prevent Returns
Reduce complaints from supply chain partners about poor quality of packaging.
Better packaging means fewer rips, spills, and split seams.
3. Lower Delivery Costs
Less packaging weight mean lighter deliveries and savings on delivery costs.
Stronger wrap means more tightly secured packaging with less bulk allowing more products to be sent in any one delivery.
4. Improve Business Prospects
Greater integrity of product packaging improves sales among end users.
Better packaging reflects on an overall higher retail reputation.
Crosslinked Polymers – Relevant Facts for Effective Packaging
Cross-linking of polymers significantly alters their properties, as shown by Alexander Chen et al (2022):
Cross links increase the strength of a film of the same thickness – by up to 30% stronger
The covalent bonds improve toughness – by up to 75% tougher – great for products with sharp edges
The chemical reactions yield hardness – up to 25% harder – good for wrapping heavy or metal objects
The Pros and Cons of Cross-Linked Polymers
The perceived benefits resulting from crosslinking, such as polyethylene crosslinking for shrink packaging, depend on the application of the material and the processing characteristics that are hoped for.
Pros of crosslinked polymers:
Increased rigidity – suitable for tough jobs
Resistance to chemical corrosion – chemical proof
Improved thermal stability – heat proof
Better mechanical strength – bend proof
Greater fluid resistance – water proof
Resistant to stress cracking – unbreakable
Lightweight – easy to move
Superior strength – tear resistance
Cons related to crosslinked polymers:
Polymers in general are not recyclable at this point in time.
During crosslinking the arrangement of the molecular chains change. There is a risk factor for physical defects.
Crosslinking can result in brittle materials
Non-crosslinked polymers are usually referred to as standard or regular polymers materials.
Advances in the plastics industry mean we have access to eco-friendly crosslinked polymers such as Ecolene® XPCR, which allows end users easy, simple disposal to reduce the environmental footprint.
Folene Packaging Offers a Full Range of Shrink Packaging, With and Without Crosslinks, to Suit All Needs.
Folene Packaging offers a full range of polyolefin cross-linked and regular shrink films. We use European-grade raw materials and produce the films locally to allow a very short turn around – as little as 2 days! Folene Packaging is there to support your packaging decisions so you can produce, package and ship with peace of mind, knowing you have checked all the boxes for superior packaging.
The Flxtite® range includes AP-1, a super high-clarity and high-gloss, stiffer film and goes all the way to AP-XF, an anti-fog film; the Ecolene® range includes Ecolene® AP-XPCR, which is made primarily from recycled materials. All our films offer top of the line sealing and shrinking properties in all directions – giving your product 360-degree protection.
Reach out to the Folene Packaging experts today for a guided tour of our range of films and get to know more about the advantages of crosslinks in polymers!
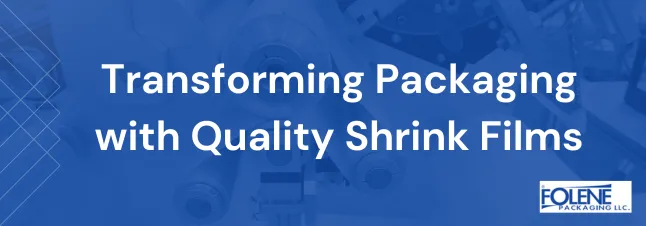